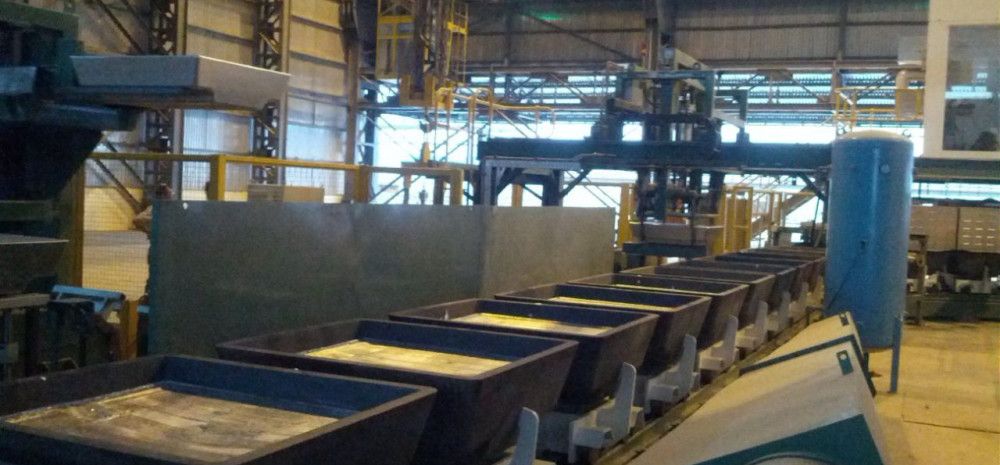
What sets o.d.t. Engineering apart from their competitors is their employees’ technical knowledge?
As a family-owned business that manufactures specialised machinery for companies such as Alcoa and Rio Tinto Alcan, their products have to be of the highest quality.
Due to the specialised, precise nature of the work, finding the right people who fit with the company culture has proved challenging, according to managing director Markus Oswald.
“We’ve always had challenges in terms of recruitment because we’ve always been a bit weird – it has to be the drawing and to the documentation, as opposed to just getting it done,” he says.
“The candidate pools are generally thinner nowadays too.
“In the past, you might have had a few candidates, contrasted them and selected one. At the moment, you find a candidate you’re comfortable with then select that one.”
In order to hire and retain the right staff, management has adopted more of a flexible workplace model.
Whereas in the past only administrative staff may have worked part time, that flexibility has now filtered through to other areas of the business, including the shop floor.
If someone is a great fit for the business but they can only work limited hours, o.d.t. Engineering makes it work.
“Ultimately it’s about what can they do for the company and what that means for the customer,” says Markus.
Machinist Glenn Shand, 52, is one employee who has benefited from the flexible workplace model.
In 2022, due to a change in personal circumstances, Glenn asked whether he could cut down from full-time to part-time work.
Glenn is an exceptional machinist who is able to work autonomously and produce high quality output.
Rather than losing such a talented worker, management granted his request. He now works three days a week and starts at 7am instead of 6am.
“The flexibility has made my life easier, otherwise I wouldn’t be here,” says Glenn. “I wouldn’t cope at the moment. This is what my mind and body is allowing me to do and management has been really good.”
In order to retain existing talent for as long as possible, o.d.t. Engineering has also transitioned several full-time staff approaching retirement to part time.
Markus says in the past three to five years, they have taken on more mature-aged employees, and it’s worked well for the company.
Indira Pather, 68, started a traineeship at o.d.t. Engineering after moving from South Africa to Australia and struggling to find employment.
Through her traineeship, Indira learned many new skills. She encouraged other mature-aged people who may have had a break from the workforce for whatever reasons to consider diving back in.
“Mature-age workers have a lot to offer – we have experience and we’re more patient than the younger ones and resilient to change,” she says.